
What is As-Built documentation and why is it so important?
Table of Contents
ToggleThe As-Built model illustrates the entire structural system in an “As-Built” condition or the way it was built. The outcome is a universal 3D model that is composed that depicts the process and the existing state of a building or facility. As-Built documentation is a crucial deliverable at the end of the project and during handover as it contains detailed documentation and technical possibility for further verification, maintenance, or renovations.
What is As-Built documentation?
Regularly recording the building progress to track the construction state can help stakeholders manage defects on the field and during operations. As-Built documentation is also used as a guide to managing building inventories and comparing data with 3D models, photos, or other 2D plans. As-Built documentation makes sure the actual state corresponds to the 3D model.
How is As-Built Documentation created?
In As-Built documentation, the site is measured using various laser scanning techniques. Terrestrial laser scanners or Drones are used to measure structural progress and build a point cloud around it. After the installation of the building services, fast and accurate scanners are used to capture the existing conditions of the project. In this way, the construction progress is monitored and recorded in stages for validation and can also be used as a digital twin.
As-Built documentation supports whom?
- Construction companies
- Building Owners
- Buyers
- Contractors
Top 5 directions through which Reality Capture has transformed the construction industry.
A myriad of stakeholders has heard and adopted reality capture to transform design and construction. Capturing accurate and quick site data for use and conversion into usable 3D models has evolved workflows. But, there are 5 crucial directions wherein reality capture has truly transformed the design and construction sector.
- Accuracy Improvements
Present-day reality capture technology makes outdated 2D and manual measurements obsolete. Cutting down on numerous site visits to verify site measurements is replaced by terrestrial or drone scans to generate a Point Cloud in a blink of an eye enriched with the highest level of detail. Accuracy enhancements have set a higher expectation bar through lower rework and reduced timelines. This supports General Contractors (GCs) to streamline and improve business workflows. Turner Fleischer Architects adopted Reality Capture to record existing conditions which led to a significant reduction in issues and change orders.
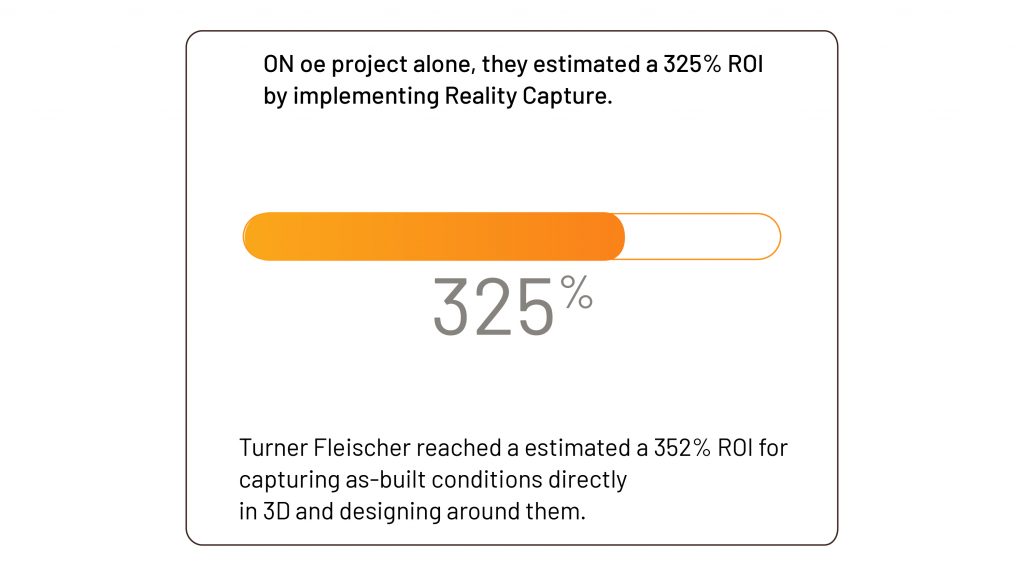
Turner Fleischer achieved an ROI of 325% by capturing As-Built conditions in 3D geometry.
- Efficiency Acceleration
Significant reduction in site visits and accelerated data collection has led to enhanced project efficiency at multiple levels. A hospital project by Bates Architects using 3D laser scanning tools encouraged 50% cost reduction. Capturing identical information via traditional methods would have caused greater numbers of site visits and higher costs.
| Marin Pastar, Bates Architects, Innovation Director quotes “ The biggest savings was the time savings – this was probably the shortest time frame project of the largest scope which Reality Capture helped us deliver.”
- Reduction in tedious manual activities
While traditional 2D CAD would involve tedious manual workflows, present-day Reality Capture manages to automate a myriad of design and construction activities. Stream of data from scanners or drones is directly fed into 3D models via various BIM software. Designs created through these 3D BIM models are fed into construction workflows leading to a reduction in tedious tasks and constructible plans. Reality Capture was deployed by McCarthy Building Companies for their construction projects and came up with a comparison vs traditional tools. Reality Capture deployed for the Stanford Hospital in Palo Alto recorded 155 scans in 13 hours (for beams, steel, and concrete floors) vs 64 hours to only scan steel camber beams via traditional methods. The comparison in survey and time savings was exponentially reinforced with accurate calculations for dimensions to create RFIs.
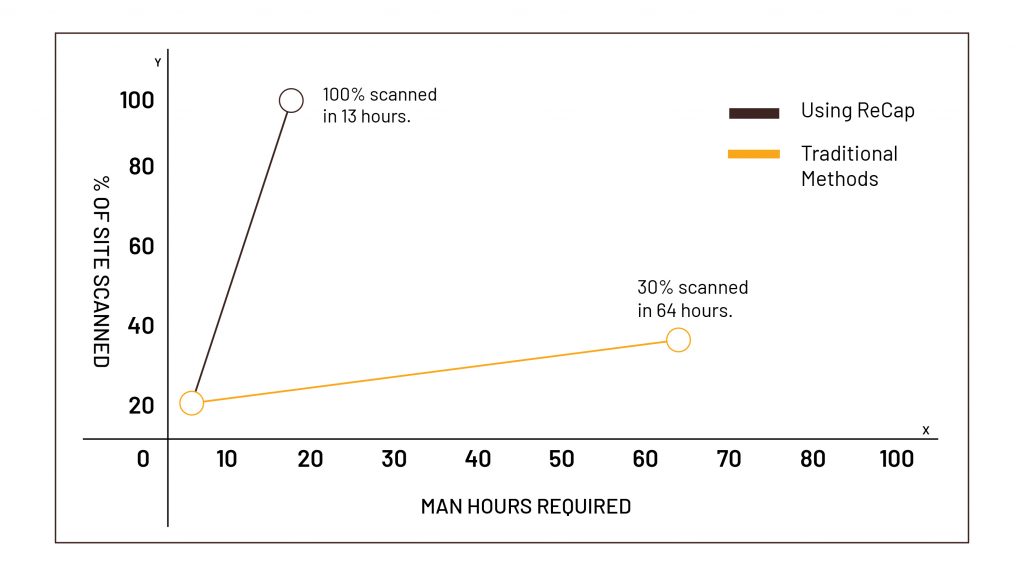
- Significant Collaboration
Easy to use Reality Capture tools and software have made it possible for global AEC firms to adopt this technology to utilize, change, share, and feed into design and construction processes. In a digital workspace, stakeholders across various project phases can record feedback, write notes, quantify site conditions, and reinforce them in existing workflows. Data streaming into 3D models in real-time makes the entire process collaborative for the entire project team.
- Construction Validation
Validating design before actual construction begins is crucial for the preconstruction stage. Making sure the design intent aligns perfectly with actual construction reduces rework by identifying problems early on. It also ensures project progress stays aligned with planned expectations.
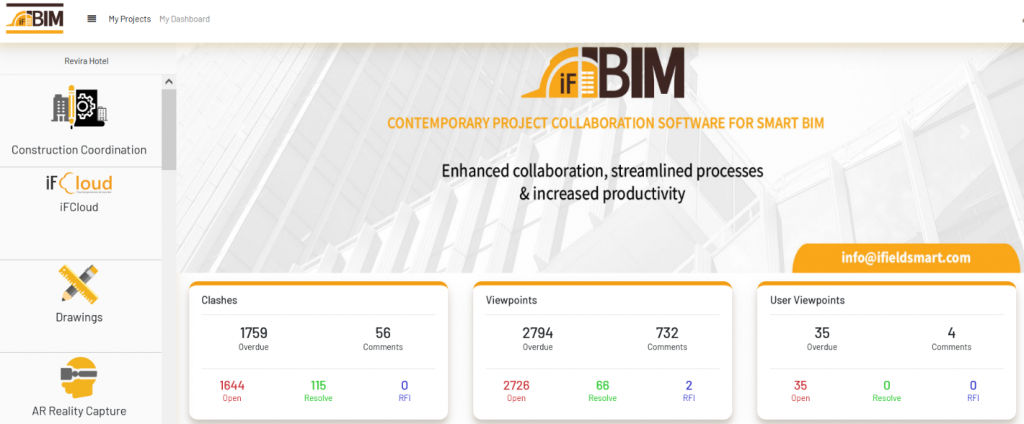
iFieldSmart Technologies supports field personnel with a single dashboard to manage all their reality capture needs for improved project coordination.
Conclusion.
BIM tools reinforced by digital As-Built documentation improve management and information control for construction projects. As-Built help detects numerous defects between planning documents and As-Built drawings. Digital visualization enriches As-Built documentation to mitigate rework and resolve issues before they even occur. Change orders can be lowered with preemptive clash visualization and resolution and accuracy through continuous improvements in productivity, efficiency, and delivery.
Reality capture isn’t new, yet the equipment, processes, and tools are superior in the present scenario. Setting yourself on construction sites with Lens360 tracking to actionable insights, managing risks, track progress is key to achieving positive onsite outcomes.
Visit Us:- www.ifieldsmart.com
You may also like
Recent Blog Post
- Best construction document management software solutions for 2025
- Revolutionizing Construction Inspections: The Power of Construction Inspection Software
- Centralized Communication and Collaboration: The Backbone of Construction Project Management
- From RFIs to Drawings: How iFieldSmart Powers Procore Workflows for End-to-End Construction Management
- Beyond Basic Sync: How iFieldSmart Supercharges Procore & Autodesk Workflows for Smarter Construction Management
Work Smarter, Not Harder
iFieldSmart empowers your team with AI-driven efficiency to simplify scheduling, boost collaboration, and keep projects on track — with human support every step of the way.